In CNC machining, two fundamental processes play a pivotal role in shaping the final product, roughing, and finishing.
Rough Machining as the name suggests, is employed to workpiece for the removal of material in bulk and shape it roughly to meet the desired form. The key feature of rough machining is its focus on productivity and high material removal rates. Roughing is followed by finishing which in CNC turning service involves the machining of a part to obtain a specific resolution.
Finishing improves the aesthetic sense of the part with improved mechanical properties. It includes machining processes such as grinding, electroplating, policing, blasting, and painting. The type of process depends on the need of the working part.
Despite its emphasis on speed and material removal, rough machining plays a crucial role in the manufacturing process. By rapidly shaping the workpiece, rough machining sets the foundation for subsequent operations, such as finishing machining, where finer details are addressed. In the finishing process, improved dimensional accuracy is targeted which is provided by sharper tools and low feed rates.
Comparison of rough and finishing machining
Both roughing and finishing in CNC turning services have different goals. The roughing process aims to give a basic shape to the working part based on the required features. Here the goal is not to achieve a smooth surface but to remove as much unnecessary material as possible with a high cutting rate.
For finishing, the surface finish and dimensional accuracy are important, and a required tolerance is obtained for the workpiece. Contrary to the roughing process, the cutting rate is deemed not important in the finishing process.
Material removal rate
Rough machining prioritizes rapid material removal to establish the basic shape of the workpiece while finishing machining focuses on achieving precise dimensions and superior surface finish. In a typical CNC turning service, the Material removal rate (MRR) is an important factor in determining the nature of the process i.e., either roughing or finishing. For a roughing process, the MRR is increased while for finishing a lower MRR is kept.
MRR is dependent on speed, feed rate, and cutting depth but for a single process, the speed is kept constant. This is because the speed of the cutting tool is chosen based on the material type, machine capacity, and vibration level which cannot be altered during the process.
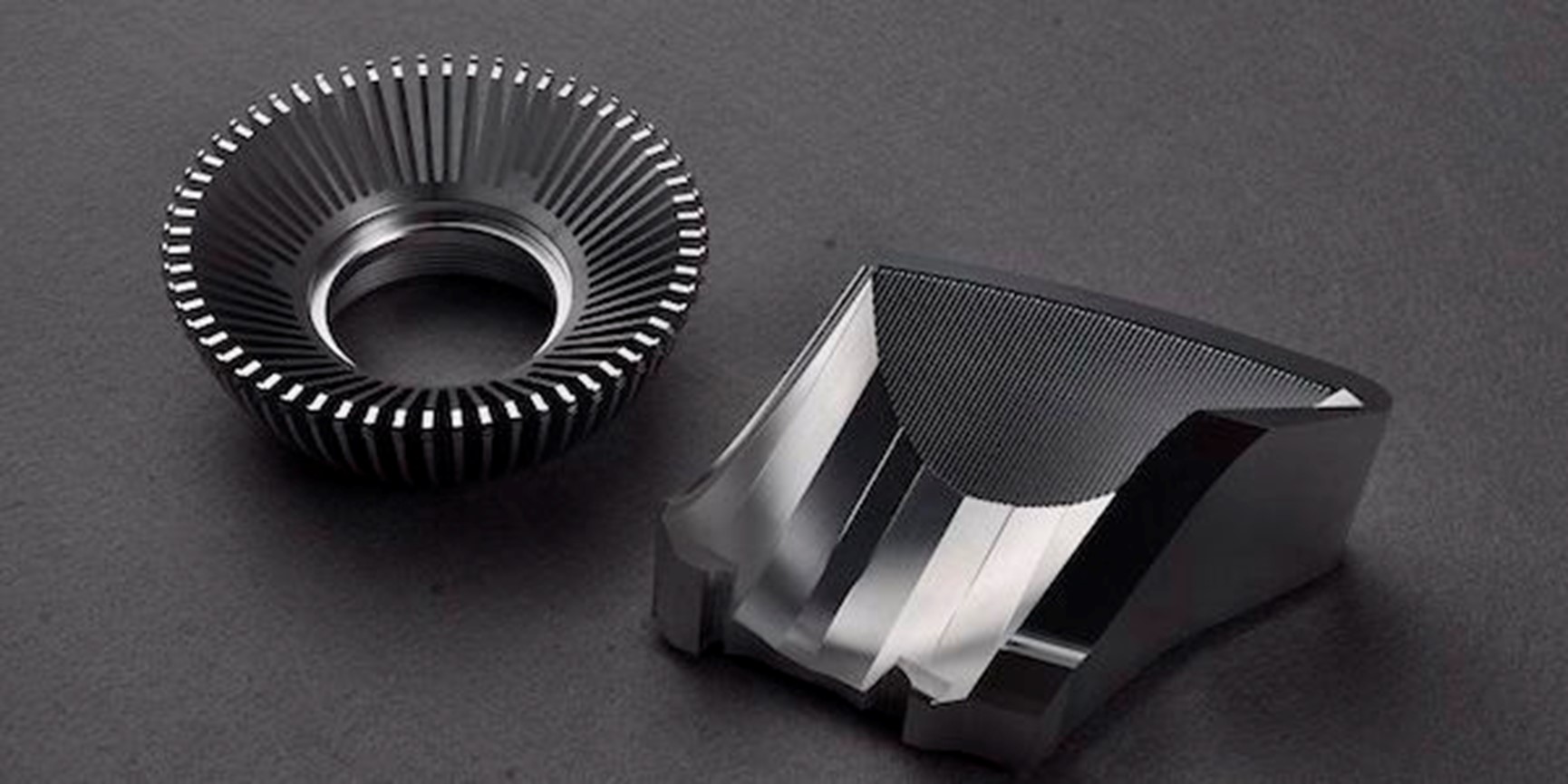
For an MRR i.e., in roughing the feed rate and cutting depth are kept high which facilitates rapid material removal while for finishing the feed rate and cutting depth are kept low resulting in a smooth and improved surface finish.
Surface roughness
The outcome of machining parameters like feed rate and depth of cut, surface roughness refers to the microscopic irregularities on a surface. It occurs in the machining process due to higher feed speed and cutting depth. An increase in feed speed and a higher cutting depth reduces the surface finish and machining accuracy of the part.
So, for roughing in CNC turning service, a higher feed rate and cutting depth are employed which results in a poor surface finish, lower dimensional accuracy, and tight tolerances. While in finishing, the feed rate and cutting depth are kept low to achieve improved surface finish, accuracy, and tolerance.
The choice of cutting tools
The choice of cutting tool plays a crucial role in achieving the desired outcome. It is used to achieve different levels of roughness by employing different cutting tools and cutting angles. For rough machining in CNC turning service, negative rake inserts are used which are capable of absorbing higher cutting force and thus achieve higher cutting speeds. For the finishing process, the positive rake inserts and front angle blade techniques are employed which results in a smooth finish and improves surface accuracy with tight tolerances. A sharp cutter is used in the finishing process to provide a refined finish to the surface.
As the feed rates are higher in the roughing process, it demands that the machines used for the roughing process are of high power, efficiency, and rigidity. The critical factor in roughing is to maintain a consistent cutting depth on the workpiece with narrow corners. Thus, it is critical to choose the right machining tool specifically tailored for the machining operation.
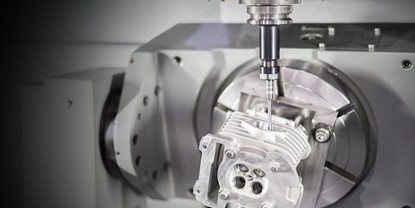
For the finishing process in the CNC turning service, the applications of the parts are considered in choosing the type of operation. For example, for automobile processes increasing the durability would be prioritized over aesthetics. Therefore, the choice of finishing process would be based on the right balance of form and function.
Conclusion
In CNC turning service, the choice of process at each stage is vital thus it becomes, critical to understand the operational principles of rouging and finishing.
DISCLAIMER – “Views Expressed Disclaimer: Views and opinions expressed are those of the authors and do not reflect the official position of any other author, agency, organization, employer or company, including NEO CYMED PUBLISHING LIMITED, which is the publishing company performing under the name Cyprus-Mail…more
Click here to change your cookie preferences